RS Production in a manual production process
Empower your operators/assemblers
RS Production help your operators and assemblers to focus and perform standardized work.
Reduce cost per produced unit
Reduce cycle time
Reduce human errors
Features
RS Production’s Operator tools becomes the user interface for the operator/assembler. It is an intuitive user interface where they will
get their workplan [ℹ️ This feature is included in RS Production OEE and RS Production ACT]
get their instructions [ℹ️ This feature is included in RS Production ACT]
perform and report quality controls [ℹ️ This feature is included in RS Production ACT]
report their work [ℹ️ This feature is included in RS Production OEE and RS Production ACT]
call for andon/support [ℹ️ This feature is included in addon Andon]
report deviations [ℹ️ This feature is included in RS Production OEE]
Also, there are real time line TV-screens.
Operator - Log in on station
Not mandatory but gives you a good traceability of who works where.
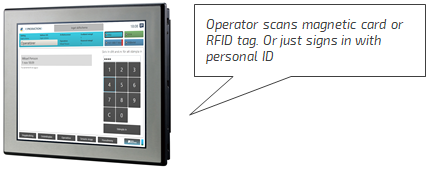
Operator - Select and start work order
Depending on what is easiest for your operators, there are some different ways to do this.
Operator manually select the production order (or type of product) on the Production Plan page
Shows next and upcoming orders. Can be configured to show only the next order (or type of product).
Barcode with both the order number and the part number
Barcode with the order number
Barcode with the part number
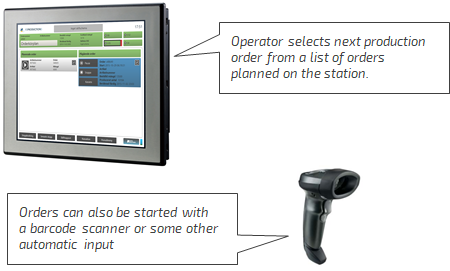
Operator follows work instructions
Directly when a new production order is started, an operator instruction will popup.
Operator instructions
Checklists
Control points and form fields
Connected files (instruction, drawing, examples) can be in different formats
owebpage, pdf, Excel, Word, CAD, video etc
Operator will follow instructions along with work. If integrated with ERP, order unique text will be shown. Operator instructions can be separated into one or more pages.
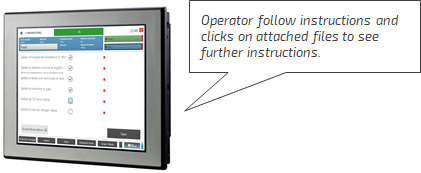
Operators registers deviations with reason codes
When operators run into problems, they register it in Operator tools using pre-defined reason codes. It can be many different things
Stoppage time (because of material, tools, equipment etc)
Quality issues (ingoing material, ready product)
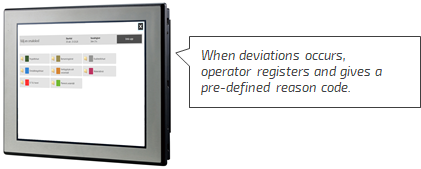
Operator makes andon call
When help is needed from an andon resource, operator pushes a button with a pre-defined message. Can be different messages for different situations.
Andond resource receives the call in the Mobile app. This can also start a char dialogue.
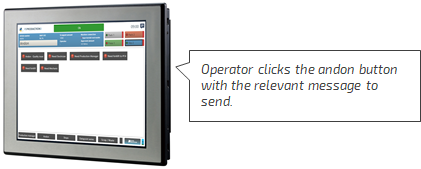
Operator registers order ready
If it is single piece production, operator registers the produced amount by just finishing the order.
If it is larger order quantities it is possible to either register amount continuously during production, or to register all amount when finishing the order.
After finishing the order, operator starts a new order and the procedure starts from the top again.
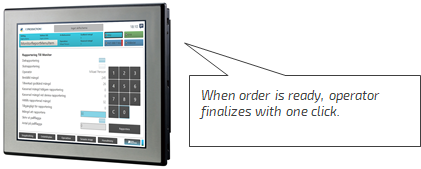
Follow status on real time TV-screens
If it is single piece production, operator registers the produced amount by just finishing the order.

OEE
The solution described above will give a OEE percentage. Together with the above solutions it is also possible to use RS Production OEE’s features for registering reasons for
Downtime (stoppages)
Speed loss (cycle times > planned)
Quality loos (scrap)'
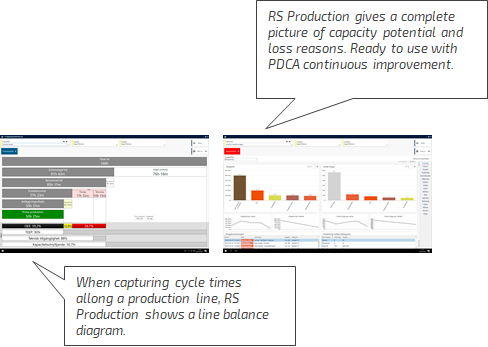
Machine signals
In manual production processes it is common to not capture any signals or data from machines or equipment.
If you can get a machine signal for a cycle counter, it can be used to automate the counting of produced amount.
If your cycle times are lower then 120-180 seconds, you can also use the cycle counter to identify stoppages automatically.
Technical setup
The typical setup is to use one measure point per station. These stations use a Windows PC of some kind
Handheld Windows PC
Stationary Window PC
Mounted Panel PC with Windows
The Windows PC needs to have an internet connection and reach the RS Production Cloud service.
RS Production is delivered as a cloud service. Real time data from the production process is captured using an Edge technology to ensure data security.
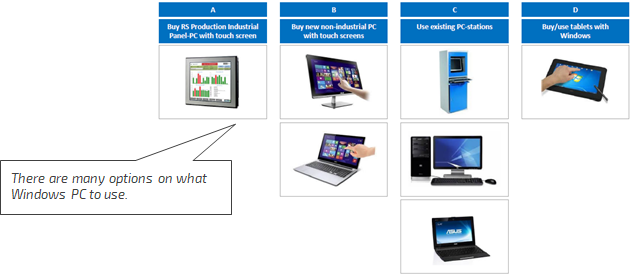