This is how you reduce energy consumption in your factory.
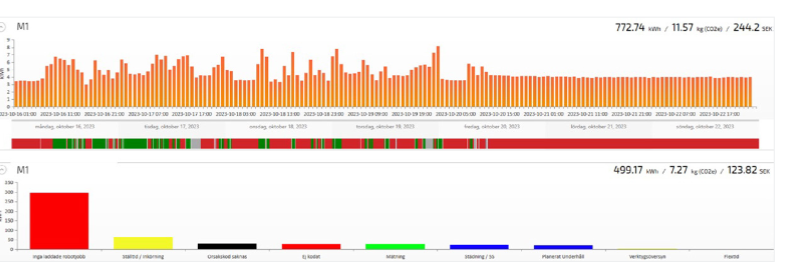
You can work according to two principles to reduce energy consumption per manufactured unit.
• More time-efficient production.
• Reduce equipment’s energy consumption.
The one does not exclude the other. The best results come from working with both at the same
time.
One way to reduce energy costs is to take measures to get by on a smaller main.
More time-efficent production
By increasing OEE by 10%, you can produce the same amount of product 90% of the time.
You will be able to turn off the production process earlier.
You get the same amount of product to deliver to your customers, and your revenue will be the
same. But you have used less energy.
Reduce energy consumption of machines and equipment (both while running and idle)
Insulating, sealing, replacing, and optimising. Production processes will take as long as before.
But you have used less energy.
More time-efficent production
This method means that by reducing unnecessary downtime in the production process (unplanned,
planned, changeovers, minor stoppages), the OEE number of the production process is increased.
The result is that the time needed to produce the required quantity is reduced.
Understand your current state
The first thing to do is to measure the time losses and give them reason codes. This is usually done
with an OEEsoftware such as RS Production OEE.
Then, you put together the follow-up of the manufacturing process time losses and energy
consumption on the same time axis.
Then, you can create a Pareto chart with OEE losses, where instead of showing time (hours) on
the Y-axis, you show energy consumption (kWh).
The diagram then shows the time losses, which to the greatest extent are energy consumption
without creating customer value.
Set goals
Set goals for energy consumption based on thecurrent and desired states.
The goal must be formulated in such a way that the team in the manufacturing process can influ-
ence it. It can be expressed in, for example, kWh per week or kWh per manufactured unit.
Control
Bring follow-up against targets of the most energy-demanding OEE losses into existing routines for
pulse meetings and weekly reviews.
Here, the teams in the manufacturing processes are then given the opportunity to be involved and
influence and come up with solutions.
Improvement process
Also, use structured improvement work. Make a gap analysis between actual energy consumptionand the current target.
Work with PDCA or similar process to develop solutions.