Better payback on your investments in machines and factories
A proven and very effective way for your factory to become more profitable and sustainable is to increase its resource efficiency.
There are two main ways to turn an increased resource efficiency into profits. Cost out and Capacity up. The right way for your company depends on your factory's strategic challenge.
Cost out strategy
If your market is saturated and there’s no market demand for you to increase your output, you will probably go for a COST OUT strategy, meaning:
Less input, the same output.
Fewer machine-hours, fewer person-hours, the same output.
Less consumed resources, the same output.
A more sustainable production process.
Lower cost per unit.
Capacity up strategy
If there is a market demand for more products than you can produce today, you will probably go for a CAPACITY UP strategy, meaning:
Same input, more output.
Same machine-hours, same person-hours, more output.
Same consumed resources, more output.
A more sustainable production process.
Lower cost per unit.
Identify efficiency losses in your production processes
In all production processes, there is a gap between the planned production time and value-adding production time.
Planned production time
The planned production time describes the number of hours you have machines turned on has machine operators ready to produce, and it means that it describes the number of hours where you have COSTS for machines and staff.
Value-adding time
The value-adding time describes the number of hours you are doing something your customer pays you for, and it means that it describes the number of hours where you have INCOMES for machines and staff.
OEE and the gap between planned production time and value-adding time
The gap between planned production time and value-adding time consists of different time losses.
Planned downtime (shift changes, meetings, maintenance).
Changeovers.
Unplanned downtime (breakdowns, lack of material, etc.).
Speed loss (machine is running, but slower than planned).
Micro stoppages (disturbances handled by machine operator).
Quality losses (rework, scrap).
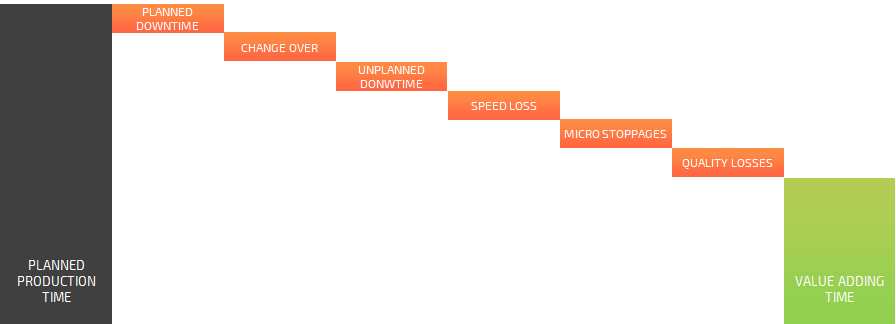
OEE is the KPI to measure the gap between planned production time and value-adding time.
Example
If you use 4 out of 8 hours to do something your customer pays you to do, your OEE is 50%. OEE calculations can be much more complex than this, but this describes the basic concept well.
OEE reveals improvement potential
Once you know a production process OEE, you also know the hidden capacity it has. If your production process’ OEE is 60%, it means that 40% of your costs for machines and staff are costs without any income.
Depending on if your current initiative is to reduce costs or if it is to increase capacity, you will look at this nonvalue adding time in different ways.
Improve nonvalue adding time in a cost out strategy
In a cost-out strategy, you keep value-adding hours while reducing planned production hours.
Creating a higher OEE and enables:
Use machines person-hours to produce the same amount.
Less fixed costs, same incomes.
Lower cost per produced unit and better margins.
Less input, the same output:
More resource-efficient.
More sustainable.
More profitable.
To reduce the planned production time and keep the value-adding time, you will have to minimize some losses.
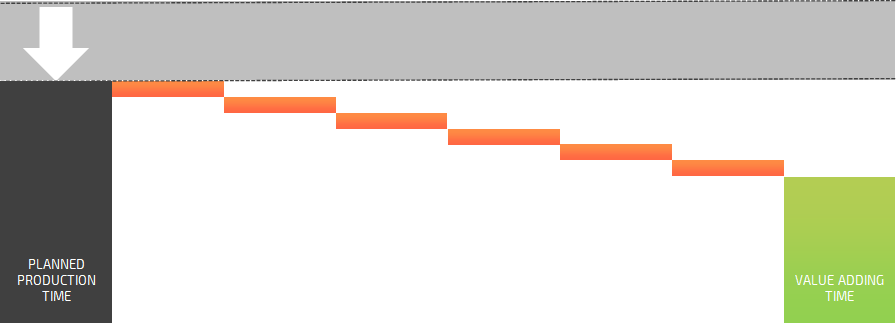
The light grey area describes the saved planned production time after OEE improvements. The orange-colored losses have been reduced. This is a direct cost saving as you still have the same output but with lower costs for machines and personnel.
Improve nonvalue adding time in a capacity up strategy
In a capacity up strategy, you want to keep planned production hours while increasing the number of value-adding hours.
Creating a higher OEE and enables:
Produce more with the same machines and person-hours.
Higher incomes, same fixed costs.
Lower cost per produced unit and better margins.
Same input, more output:
More resource-efficient.
More sustainable.
More profitable.
To increase the value-adding time and keep the planned production time, you will have to reduce some losses.
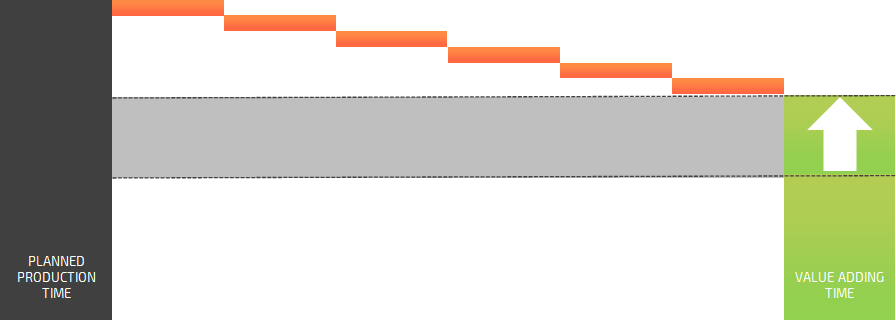
The light grey area describes the new capacity opened after OEE improvements. The orange-colored losses have been reduced. The newfound capacity can be used to increase output with the same fixed costs for machines and staff. Resulting in that the new capacity will have no additional cost for machine hours or person-hours.
Love your losses. They are your improvement potential
To make this happen, you will need an improvement culture. Your team will have to search for losses every day because they are your stepstone to the next OEE improvement and, therefore, one step closer to your company’s target.
A modern OEE tool helps you find improvement potential and make it obvious for everyone from machine operators to owners.
Processes and methods for continuous improvements
There are a few basic processes and methods for manufacturing companies that seriously want to increase OEE and enable better results.
Escalate ongoing losses for quicker reactions. RS Production OEE can help you with this.
Daily pulse meetings help everyone get a standardized overview of top losses (e.g., losses with the greatest improvement potential). RS Production OEE enables you to summarize your losses, and Boards on Fire helps you with digital boards.
Use a structured improvement process (like PDCA, A3, etc.) with root cause analysis and prioritize the improvement actions that give you the most “bang for the bucks.”
Standardize on your best practices and spread amongst all operators and team members. Tools like RS Production ACT can help you with this.
Follow up on improvement activities and celebrate together.